Background
In June 2016, the Toronto and Region Conservation Authority (TRCA) Board of Directors approved the construction of a new administrative office building at 5 Shoreham Drive in Toronto and directed staff to take the necessary action to complete the project. The resulting four-storey mass timber building was intended to be one of the most energy-efficient office buildings in North America, featuring sustainability aspects such as solar thermal panels on the roof, four solar chimneys, water walls to reduce energy use, electric vehicle charging stations, rainwater harvesting to irrigate a green roof, permeable pavement, and more!
Read more about the sustainability features of TRCA’s new administrative building.
Fast forward to February 2024, with the construction of the new office building nearly complete, the next phase of the project was to identify which items from the old office were to be moved to the new one and which items would stay behind and require reuse solutions.
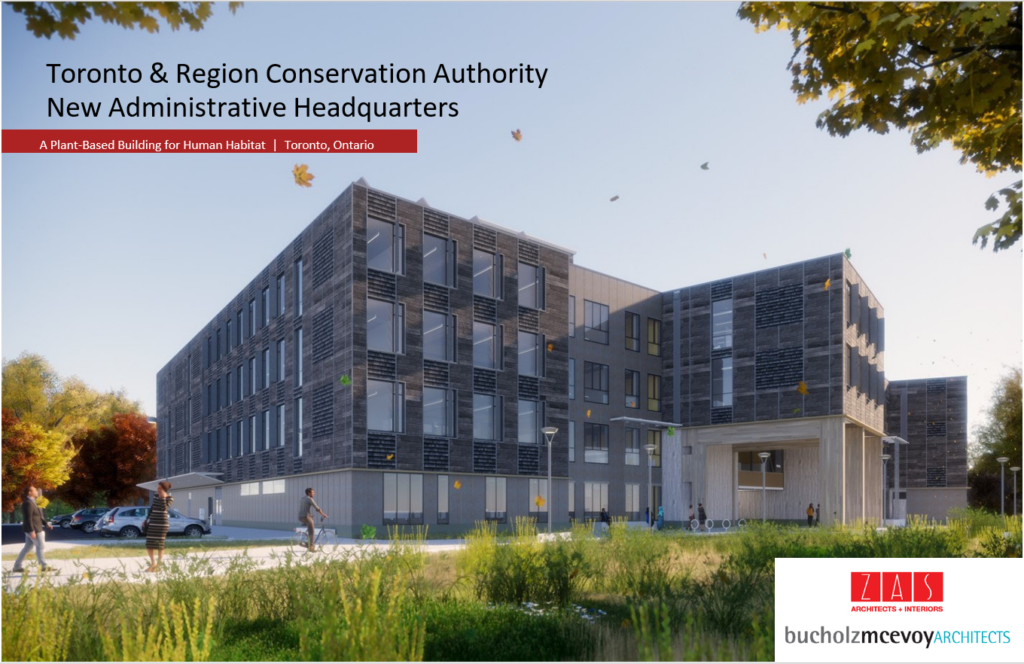
Scope of the Project
The goal of the project was to enhance the sustainability of the new head office by maximizing the diversion of solid waste that would have been generated during the relocation, preventing it from ending up in the landfill.
To achieve the goal, the following steps were taken:
Project Team
An internal cross divisional project team was formed which consisted of TRCA’s Property and Asset Management and Partners in Project Green (PPG) teams.
Visual Audit
The project team first conducted a visual audit of the two-story office building that had been rented while the construction of the new office was underway. The purpose of this exercise was to identify the types of furniture, office supplies, and equipment that would not be moved to the new head office and would need to be rehomed.
Collection of Small Items
The second step was to set up a process to collect and organize small items such as file folders, binders, desk organizers, and writing instruments from different divisions within the office. Collection bins were set up in common areas (lunchrooms, kitchenettes, printer rooms) and communications were sent to all internal TRCA departments with instructions on what to put in the bins while furniture was tagged by TRCA’s Property and Asset Management team.
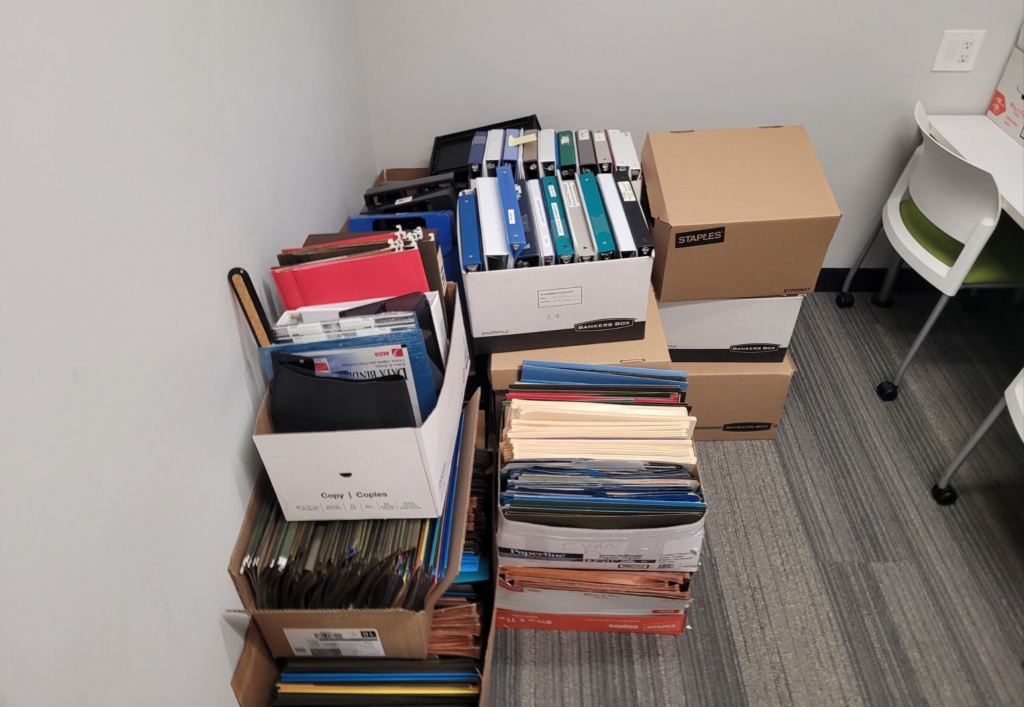
Inventory
The third step was to create an inventory (to track the quantity and type of materials) that would be shared with internal and external groups and for reporting metrics. After all the items had been tagged and collected, the inventory tracked each item by logging the quantity of items by type, key characteristics such as dimensions and colour, and pictures were taken with the help of TRCA staff volunteers.
Note: Download PPGs Inventory Template to organize your next renovation project.
Solution Finding
PPG’s Material Exchange (MEX) program played an integral role in finding a new home for the leftover items such as office supplies, electronics, and furniture. PPG reached out to its active network of organizations open to receiving materials for reuse and identified organizations and individuals who were interested in reusing the smaller items. The Peel District School Board’s Creative Zone, the Toronto Catholic District School Board, and the City of Toronto were keen to reuse the many office supplies that were available. This included 753 small binders, 710 file folders, 62 book ends, and 114 desktop organizers that would be used by students and teachers. Lastly, the Electronic Recycling Association (ERA) supported the responsible recycling of 40 pieces of IT equipment.
With regards to large items such as furniture, fridges, and televisions, about 122 items were moved out of the rented building within a 30-day span in response to the termination of the lease with the landlord. All items, except for one cabinet which was taken by a local resident, were collected and used internally by various TRCA sites, including parks facilities, education centres, and satellite offices.
The effective collection and reuse of items by TRCA staff was largely due to the immense advanced notice about upcoming surplus furniture to TRCA staff in informal conversations, which began in 2022. In addition, communications were distributed by the Senior Leadership Team to their respective Divisions after receiving 30 days’ notice to vacate the premises. Following the notice of available surplus materials, TRCA staff were able to claim items via email or Microsoft Teams and pick up items at their convenience. TRCA’s Property and Asset Management team coordinated these pickups. Staff proved to be very resourceful by bringing their own tools and extra brackets to dismantle and repair broken items such as tables so they could be reused.
Key Metrics
Over a three-month period, an estimated total of 8.15 tonnes of material were diverted from the landfill, saving the receiving organizations and various TRCA sites around $122,000 if they were to buy the same items new. Since items were not sent to landfill, 1.15 tonnes of CO2e were avoided, which is equivalent to 2.6 barrels of oil being burned (source: Natural Resources Canada, Greenhouse Gas Equivalencies Calculator). TRCA also saved money by avoiding waste collection and tipping costs (about $1,110).
The above figures are estimations of the amount of material collected and their impact. The tonnage and cost of each item type was determined by the results of online searches of similar items, while the estimated greenhouse gas (GHG) emissions were calculated in metric tonnes of carbon dioxide equivalent (CO2e) using the United States Environmental Protection Agency’s Waste Reduction Model Version 15 (WARM) tool. The data has not been adjusted to Canada-specific GHG emission factors. This data should only be used to measure broad impacts and trends from waste diversion actions.
A noted measure of success was that nearly all materials in the two-storey rented building were reused, thereby avoiding any material being sent to landfill. The only items that were sent to landfill were a few binders larger than 2 inches in which receivers could not find a reuse for.
Lessons Learned
Completing a move of this scale requires a dedicated team to support the organization, communication, and documentation of each step of the process. This proved challenging for a small project team who were required to balance other projects simultaneously. Reflecting on this experience, the project team noted that it would have been beneficial to have a larger team that could manage different aspects of the project (e.g., one person focused on sorting, buying and distribution of chairs). Since this was not feasible, a call for internal volunteers was made to help support the sorting and quantification of items.
A key learning for the team was the importance of creating and maintaining an accurate inventory of reusable materials and updating this list as materials are being identified. Doing so increased the efficiency of the project team, helped them stay organized and prevented materials from accumulating haphazardly. The inventory also allowed for better communication with potential receivers of the materials and tracking metrics to communicate the scale and impact of the project.
Another important learning was the value of clearly labelling the collection bins and communicating to staff on how to handle materials that do not align with the designated collection categories. This allowed for proper sorting of materials. These practices established efficient processes which increase the replicability and scalability of similar projects in the future.
Overall, the project proved to be a great success in diverting nearly all identified reusable materials from the landfill while benefiting both internal and external groups. This not only resulted in reduced GHG emissions generated from landfill waste but also lowered the embodied carbon from new products, in addition to cost savings for all parties involved.
_____________________________________________________________________________
Partners in Project Green’s Material Exchange program facilitates the exchange of material generated within our stakeholder community (businesses and non-profit groups) to divert waste from landfill, move towards a circular economy, and strengthen community ties. To learn more about the Material Exchange program, please contact Darlene.Coyle@trca.ca